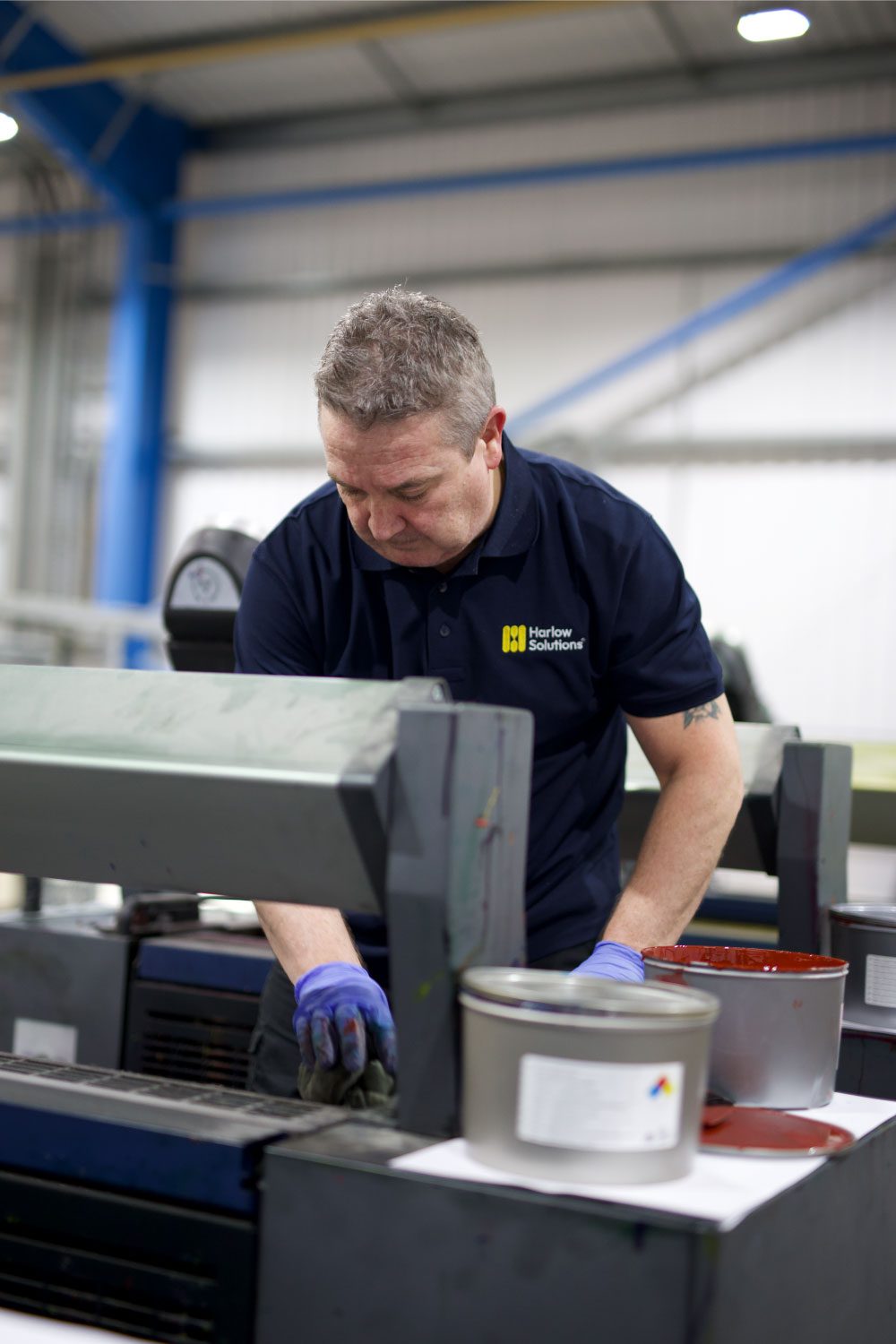
Print quality plays a huge role in pharmaceutical projects. Everything, from medication labels to patient information leaflets, must be clear and accurate. Optimal printing not only impacts how the information is read but also ensures it’s understood correctly. This can directly affect patient safety and help prevent medication errors.
Clear and accurate printing is crucial for compliance too. Pharmaceutical companies must follow strict regulations to ensure their products are safe and effective. High-quality printing helps meet these standards by providing precise and readable information. Errors in labels or instructions can lead to serious consequences, including legal issues and harm to patients.
Using advanced printing techniques can significantly enhance the quality of printed materials. Lithographic and digital printing methods offer high-resolution results, making sure every detail is sharp and clear. Specialised print finishing options add an extra layer of quality, ensuring the durability and readability of pharmaceutical documents. By choosing the right printing solutions, pharmaceutical companies can maintain high standards and ensure the safety and satisfaction of patients.
The Role of Advanced Printing in Pharmaceutical Projects
Print quality is critical in pharmaceutical projects. High-quality printing ensures that important information, such as dosage instructions, warnings, and batch numbers, is clearly visible and easy to read. This precision helps healthcare professionals and patients follow the correct guidelines, reducing the risk of medication errors. When information is printed accurately, it enhances trust in both the product and the company.
Accurate printing directly impacts patient safety and compliance. Pharmaceutical packaging and labels must meet strict regulatory standards to ensure they provide the necessary information for safe use. Any error or smudge in the print can lead to misinterpretation, which could be harmful. Clear, accurate printing helps to ensure that all compliance requirements are met, thereby safeguarding patient health and well-being.
Failing to maintain high print quality can have serious consequences. Poor printing can result in critical information being unreadable, potentially leading to misuse of medication and adverse health effects. Additionally, it might also mean failing to meet regulatory requirements, resulting in legal repercussions or loss of trust in the brand. Therefore, focusing on superior print quality is not just a choice but a necessity for pharmaceutical companies.
Types of Advanced Printing Techniques for Pharmaceuticals
Lithographic and digital printing methods play major roles in pharmaceutical printing. Lithographic printing, also known as offset printing, is ideal for high-volume runs. It delivers consistent, high-quality prints and is cost-effective for large batches. Digital printing is more suitable for shorter runs and allows for quick changes and customisations. Both methods offer reliability and high resolution, essential for clear and precise pharmaceutical print needs.
Wide-format printing offers substantial benefits for large-scale projects. This technique is used for printing on larger surfaces and is excellent for creating posters, banners, and large labels that are often used in pharmaceutical marketing and packaging. Wide-format printing ensures that even the smallest details are not lost, which is essential for clarity and readability in pharmaceutical materials.
Specialised print finishing options add an extra layer of quality and durability to pharmaceutical prints. These can include varnishing, laminating, and embossing, which protect the printed materials from wear and tear. Specialised finishing also gives a professional look to packaging and promotional materials, enhancing brand appeal and ensuring the printed information remains intact and legible during handling and transportation.
Enhancing Compliance and Safety Through Advanced Printing
High-quality printing is esse for meeting regulatory compliance in the pharmaceutical industry. Regulations demand that all product information be clear, legible, and durable. High-quality printing ensures that labels, packaging, and inserts meet these strict standards. This accuracy helps avoid fines or recalls and ensures that patients receive the correct medication and instructions for use.
Secure printing plays a vital role in preventing counterfeiting. Counterfeit medications pose a significant risk to public health, and secure printing techniques make it harder for counterfeiters to replicate packaging and labels. Features like holograms, special inks, and unique barcodes help verify the authenticity of pharmaceutical products, protecting both consumers and brands.
Accuracy in printing dosage instructions and labels is of utmost importance. Incorrect or unclear dosage information can lead to medication errors, which can have serious health consequences. High-quality printing ensures that critical information, such as dosage, usage instructions, and warnings, is printed clearly and accurately. This precision helps healthcare providers and patients use medications safely and effectively.
Best Practices for Implementing Advanced Printing in Pharmaceutical Projects
Selecting the right printing method for specific projects is essential. Lithographic printing is suitable for high-volume batches with consistent quality, while digital printing offers flexibility for smaller runs and quick adjustments. Evaluating the specific needs of each project, including volume and customisation requirements, will help determine the best printing method to use.
Ensuring quality control in print production involves several steps. Regularly inspecting printed materials for accuracy and clarity is crucial. Implementing stringent quality checks at various stages of the printing process helps catch and correct errors early. Additionally, using high-quality materials and maintaining well-calibrated equipment contribute to consistent print quality.
Integrating printing with digital record-keeping enhances traceability. By linking printed materials to digital records, it becomes easier to track and verify each batch of products. This integration helps manage recalls and audits efficiently, ensures compliance with regulatory standards, and improves overall accountability in the production process.
Conclusion
Advanced printing solutions offer numerous benefits for pharmaceutical projects. High-quality, accurate printing ensures that critical information is always clear and legible, enhancing patient safety and regulatory compliance. Secure printing helps prevent counterfeiting, protecting both consumers and the pharmaceutical brand.
Working with the right printing partner and maintaining strict quality control measures are vital for the successful implementation of advanced printing solutions. Additionally, integrating printed materials with digital records improves traceability and accountability, facilitating efficient management of recalls and audits.
Pharmaceutical companies should strongly consider partnering with the right printing service provider to enhance their operations. At Harlow Solutions, we are committed to providing innovative digital and bulk printing solutions tailored to the needs of the pharmaceutical industry. Contact us today to learn how our advanced printing services can support your projects and ensure compliance and safety.